External Side Of The Mold
- The locating ring should have a diameter of 100mm±0.1mm0.1mm and fastened with 4 screws M8
- Clamping plate material is 1730
- Mould size should be 5mm less than tie bar of injection machine
- Mould should with 4 support pin, size :¢50 mm * length 100 mm.The support must be recessed mould 10 mm
- The mould ship with install SKS name plate
- The location of the bolt hole should allow the movement of the mold (open or closed) perpendicularmente to the ground. All of the plates should possess 4 holes with thread M20x40 to facilitate the movement during the maintenance and M12 for the ejector plates
- POSITION OF THE HOLES FOR TRANSPORT
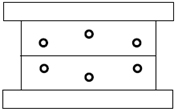 Mould weight within 1500kg,Allow 2 Hoist holes for Assemble Mould Mould weight exceed 1500kg,Must be with 4 Hoist Holes for Assemble Mould
- See Follow Pic-Lock for mould
Purpose:Ensure Mould safety Assemble Assemble Way:Fix On mould plate with M10 screw
- Mould needs to coat with derusting agent, guide post and other slide parts could use grease for lubricating. The mould external also use derusting agent, and packaged with PVC film. The loaded wooden box needs fumigation
- Provide 2D assembling drawings, part drawings,3D drawings, delivery checking list,mould inner photos, external photos, all the documents CD copy, mould drawings should be printed, and detail delivery standards please refer to SKS delivery standard explaination
- The supplier should provide 30% spare parts of easy damage components(such as ejector pin,air valve,spring,etc)
Runner system
- If mould in cold runner. The sprue brush must be HRC56-58
- Sprue radius according SKS injection machine standards..
- If mould in hot runner ,it should be according SKS request. All hot runners must be ship with sprue brush and thermocouple.
- The hot runner manufacturer need to offer a whole set drawings according to injection system
- The connector box should be fixed on the plate under top claming plate but could not directly fixed on the clamping plate
- The hot runner connector socket use YUDO standard But on special situation, use PHOENIXCONTACT 24 pins connector socket, Type: HC-B 24 ESTS 编号:1770749
- To put insulating plates among the plates supports, to reduce the thermal dissipation
Components
- Mould cooling channel diameter 10mm, male/female connector use HASCO, be recessed in the mould, countersink size Ø32x25mm.
Nate: the Inlet or Outlet should be marked on the mould(like In1 Out1), whether it needs water collectormanifold depend on mould requirement.
- Moveable parts of mould, temperature control should be independent control.
- Hydraulic parts(oil hydraulic, motor etc) use Junfan standard Taiwan
- Connector of oil channel use REXROTH ,Type:MD-007-2-WR017-19-1 3/8"
- The oil channel should be fixed inner side of mould, use drill hole instead of oil pipe, the external side must not have oil pipe. The oil channel connector block.Should be fixed on the opposite of operation side
- Stroke switch use : Schneider。Type: XCMD 2 102L1.
- On special requirements, the mould needs counter.

Others
- Fan air vent should be on the cavity parting line, width 5mm, depth: 0.04mm, gap: 12mm, venting mouth to parting line needs 2mm distance, no through.
- All the sliders should have temperature adjusting system
- Ejector plate at least 30mm thickness, must have down guide post and guide bush. If the length less than 750mm, use 4 pcs down guide post, use mechanical ejector resetting. If the length larger than 750mm, use 6 pcs down guide post, use oil hydraulic ejector resetting
- All the moulds should be automatic without any special requirements.
- The wear plate should use H13 steel, vacuum quenching HRC56-58, should have oil groove, as follow shows: The wear piece of the clamping face should be recessed in the mould
- The mould should have 4 guide post design, and one should be on 2mm eccentric situation, and avoid mould 180 degree assembling.
- The mould should have transparent anti-dust installed on the each side of ejector plate
- The ejector return should be connected with pull rod of injection machine,
thread M16
- Not Permit have sink mark, scratch, incrustation….on the mould surface
- with the mould you have to supply the drawings about the outline of the circuit
- Operate side required with TOP Name plate
- Each mould plate require Mark No. …such as S50C
1
Require of project
To be reviewed by customer before Tool kick off 2D assy drawing in 3 view + ISO picture Dimension on tool Weight on tool Part weight Decription on ejector system Detail decription on coolingsystem Estimated cyclus time Tooling schedule , 1 Excel sheet pr tool , show design time , manufacture process steps ,T1 , T2 , Shipping Project plan include all tool , show design time , T1 , T2 , Shipping
To be deliver weekly Updated tooling schedule Picture of latest status (EACH TOOL!!) Decription on delays if any and a CAR of how to catch up schedule again IMIDIATE respond, a revised schedule and if any cost related from supplier in case of delay caused by PT.
To be deliver for T1/T2 Samples Trial report include quality report include picture of problem with part (each part) Trial report include quality report include picture of problem with Tool (each tool) Molding trial parameter Trial report show min 20 shot + 100 dry cyclus + 20 shot Movie of min 10 shot full automatic cyclus update status every Monday and Thursday in Excel sheet report
To be deliver before tool shipping Picture of all tool before packing Packing instruction include spec for oil is used to prevent rust Spec of packing material Packing instruction Tooling manual for maintainance and repair Molding parameter |